How to Build a Successful Apprenticeship Program in Manufacturing
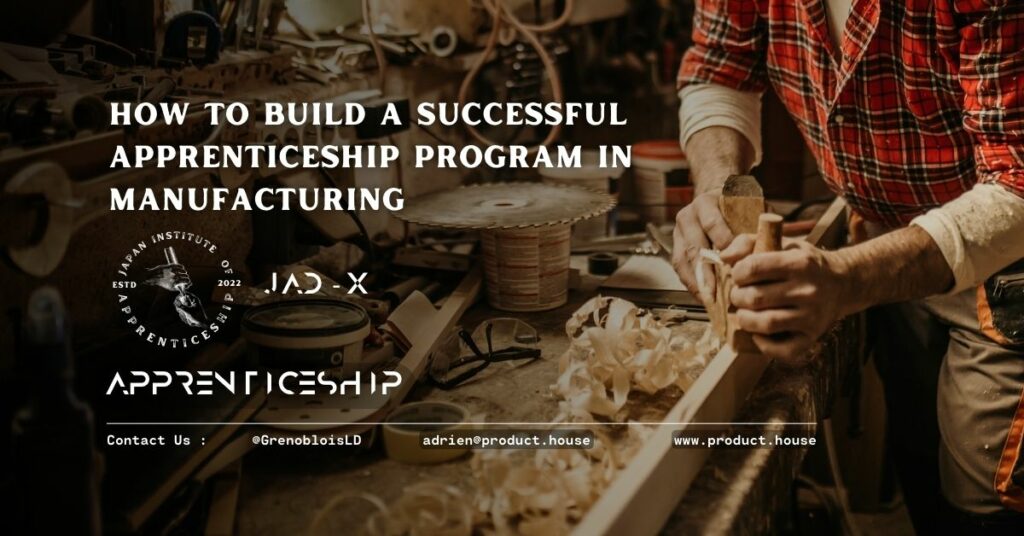
Manufacturing is a key industry in many countries, providing jobs and contributing to economic growth. However, many manufacturers face challenges when it comes to finding skilled workers to meet the demands of a rapidly changing industry. Apprenticeship programs can be a great way to address this issue and build a skilled workforce for the future.
If you’re a manufacturer looking to start an apprenticeship program, here are some key steps to help you build a successful program:
- Identify your needs and goals The first step in building an apprenticeship program is to identify your needs and goals. What skills are currently in short supply? What skills will you need in the future? What are your long-term business goals? Answering these questions will help you create a program that addresses your specific needs.
- Develop a structured training plan Once you have identified your needs and goals, it’s time to develop a structured training plan. This plan should outline the skills and competencies that apprentices will need to acquire, as well as the steps they will take to achieve them. It’s important to make the plan clear and easy to follow, so that apprentices understand what is expected of them.
- Find the right apprentices Finding the right apprentices is essential to the success of your program. Look for candidates who are motivated, eager to learn, and have a strong work ethic. You can recruit apprentices through schools, vocational training centers, and job fairs, among other channels.
- Provide hands-on training Manufacturing apprenticeships are all about hands-on training. Make sure that your apprentices are given ample opportunity to practice their skills in a real-world setting. This will help them develop their skills and gain the confidence they need to succeed.
- Offer ongoing support Support is key to the success of any apprenticeship program. Make sure that your apprentices have access to mentors, trainers, and other support staff who can help them throughout their apprenticeship. Regular feedback and performance evaluations are also important for tracking progress and identifying areas for improvement.
- Build partnerships Building partnerships with other manufacturers, industry associations, and educational institutions can help you expand your network and stay up-to-date on best practices in the industry. Partnerships can also provide opportunities for apprentices to gain exposure to different aspects of the industry.
- Evaluate and improve Finally, it’s important to evaluate your apprenticeship program on an ongoing basis. Regular evaluations can help you identify areas for improvement and make necessary changes to the program. As your business and the industry continue to evolve, your apprenticeship program should also evolve to meet changing needs.
Manufacturing Specifics vs Other Industries
Specific Considerations for Manufacturing Apprenticeships:
- Hands-on training on machinery and tools specific to the manufacturing industry
- Safety training and protocols specific to manufacturing facilities and equipment
- Introduction to industry-specific software and technologies, such as CAD (computer-aided design) software
- Understanding of production processes and workflows in a manufacturing environment
- Knowledge of quality control and assurance methods for manufacturing products
- Familiarity with supply chain and logistics management in a manufacturing setting
- Exposure to different manufacturing specialties, such as CNC machining, welding, and sheet metal fabrication
Specific Considerations for Service Industry Apprenticeships:
- Understanding of customer service principles and best practices
- Training on software and technology specific to the service industry, such as point-of-sale systems
- Familiarity with service-specific regulations and laws, such as health and safety regulations in the food service industry
- Knowledge of service-specific skills, such as menu planning and food preparation in the culinary industry
- Exposure to different service specialties, such as catering, event planning, or hospitality management
A Little Glossary as a Reminder
- Apprenticeship: A structured training program that combines on-the-job training with classroom instruction to teach the necessary skills for a specific occupation.
- Journey worker: A worker who has completed an apprenticeship program and is recognized as being fully trained and qualified in their trade.
- Trade: A skilled occupation that typically involves manual work and requires specific technical knowledge and abilities.
- Competency-based training: A training approach that focuses on specific job-related skills and knowledge, rather than a fixed period of training.
- Work-based learning: A training approach that involves hands-on learning and training on the job.
- On-the-job training: Training that takes place at the workplace, where the apprentice learns skills by working alongside experienced workers.
- Classroom instruction: Training that takes place in a classroom or other formal setting, where the apprentice learns the theoretical and technical aspects of the job.
- Training plan: A structured plan that outlines the goals, learning objectives, and training activities for an apprenticeship program.
- Mentor: An experienced worker who provides guidance and support to an apprentice, sharing their knowledge and expertise to help the apprentice learn and grow in their trade.
- Technical skills: The specific knowledge and abilities required to perform a skilled occupation, such as operating machinery or using specialized tools.
- Soft skills: The personal qualities and abilities that help workers communicate, collaborate, and work effectively with others, such as problem-solving, time management, and teamwork.
- Industry standards: The benchmarks and requirements that define the expectations for a specific occupation or industry.
- Credential: A certification or qualification that indicates an individual’s competence and proficiency in a specific occupation or industry.
- Certification: A formal recognition of an individual’s knowledge, skills, and abilities in a specific occupation or industry, typically awarded by a third-party organization.
- Apprenticeship agreement: A legally binding agreement between the employer, apprentice, and training provider that outlines the terms and conditions of the apprenticeship program.
In conclusion, building a successful apprenticeship program in manufacturing requires careful planning, dedication, and ongoing support. By following these key steps, you can create a program that meets the needs of your business and helps you build a skilled workforce for the future.